Boring tools
Sutton Tools UK Offers a Range of Specialist Boring Tools and Boring Bars For the Automotive, Aerospace, Marine, Agricultural and Heavy Plant Industry
Our choice of specialist boring options range from standard boring bars to micro boring tools, to specialist technology for small micro boring applications or bespoke specials. Whatever your boring tool requirements, as UK distributors for Rigibore, Sutton Tools UK can offer the right solution.
Zenith Boring Tool
Zenith is Rigibore’s total automation solution to producing micron accurate bores. This innovative solution offers unparalleled savings and a tangible return on investment by reducing labour costs, eliminating scrap and supporting 24-hour production through lights-out manufacturing.
The Zenith system will integrate an ActiveEdge Boring tool with in-process measurement to enable a machine controller to automatically compensate for insert wear, temperature changes and material inconsistency without manual intervention and without stopping the manufacturing process.
This is also known as closed-loop compensation. Therefore, allowing organisations to meet precision tolerances and production target in a consistent and repeatable manner.
Zenith Benefits:
Accelerate Productivity
Removes Operation Intervention
Eliminates Scrap
Improved Process Control
Reduced Cycle Time
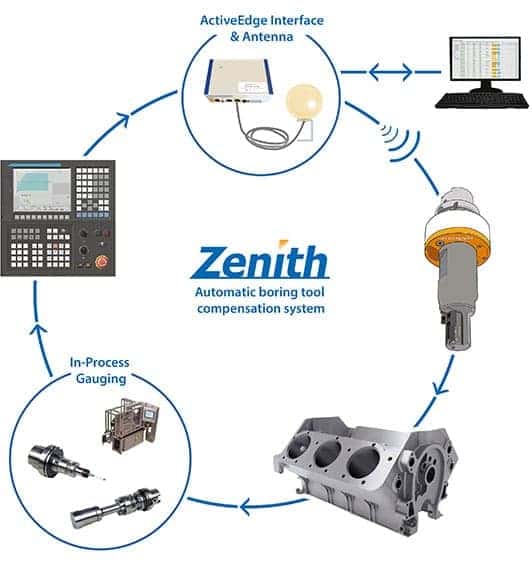
Active Edge Boring Tool
ActiveEdge offers simple and precise wireless adjustment, allowing micron accurate diameter changes at the push of a button.
Simply entering the tools unique ID and a compensation request into the ActiveEdge Remote Control allows independent adjustment of up to seven ActiveEdge cartridges on a single tool through wireless transmission.
The ActiveEdge boring bar suits any taper shank, spindle connection or adapter as required.
ActiveEdge Benefits:
Micron Accuracy
Reduced Cycle Time
Health and Safety Improvements
Simplicity In Adjustment
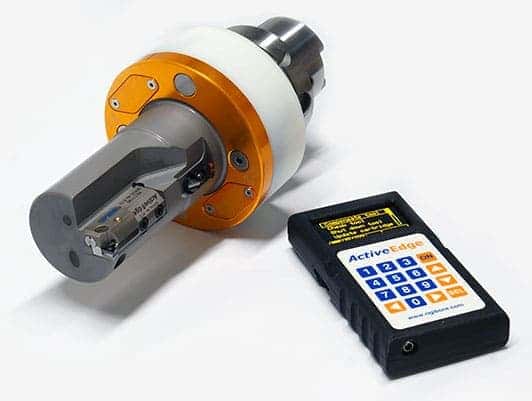
Smartbore
Rigibore’s patented Smartbore system, allows fast, simplistic and micron-accurate ‘manually operated’ cutting-edge tool adjustments without removing the tool from the machine. Thus, enveloping from a diameter range of 16mm upwards.
Precision Smartbore cartridges adjust at the twist of the wrist, using the Smartbore Digital Adjuster. The micron-accurate changes display clearly on the LCD screen of the Adjuster, consequently ensuring operators of all skill and experience levels can meet critical tolerance requirements.
Multiple Smartbore cartridges can be manufactured on a single tool, allowing multiple diameters to be machined simultaneously, subsequently reducing cycle time significantly. Smartbore’s design flexibility allows cartridges to be manufactured as a built-in solution, or as replaceable cartridges.
Smartbore Benefits:
Single or multi-feature tooling capabilities
Reduce spindle downtime
Minimised cycle time
Micron-accuracy maintained regardless of varying skill levels
Cartridge adjustment down to 0.6mm (1 micron)
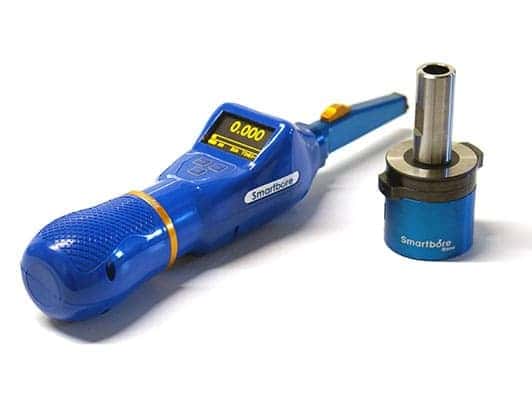
Smartbore nano
Rigibore’s Smartbore Nano combines simplicity and precision to excel on small hole boring operation. The Smartbore Nano digital fine boring head covers a boring range from 0.5mm-16mm on diameter, with precision adjustment of 0.001mm.
The design also applies patented Smartbore technology to perform precise diameter changes, using the handheld Smartbore Digital Adjuster. The dynamic design reduces downtime in operation, as well as improves finish quality and allows operators to meet precision tolerances without clamping in adjustment.
Smartbore Nano’s functional design houses electronic components in the Smartbore Adjuster, therefore keeping sensitive electronics outside the working environment. This removes the risk of tool damage from collisions with chips or coolant, as well as reducing unit costs on operations with multiple heads.
Smartbore Nano Benefits: –
Reduced spindle downtime
Reduced cost on multiple boring heads
Simplistic digital adjustments
Eliminates Vibrations
Allows insert changes to support ant material grade for the application
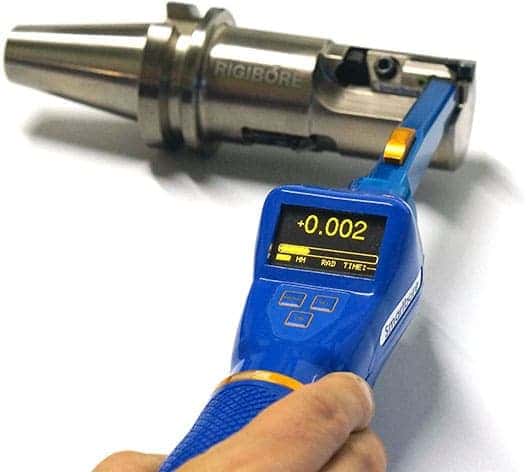
Special Boring Tool Capabilities
Rigibore is a world leader in the manufacture of custom or multi-feature boring tools. With decades of knowledge and experience, we design and manufacture special tooling to achieve our customer’s production objectives. Hence, our engineering expertise can reduce cycle time, improve part quality and process reliability, in addition to reducing overall tooling costs.
A fast quotation service (typically 24 hours) is standard for special tooling, undoubtedly made possible with RADS, Rigibore’s tool design software. RADS can manufacture combination boring tools, furthermore allowing customers to machine multiple concentric features in one machining operation. This design capability contributes to a greatly reduced cycle time, in light of performing roughing and finishing operations in one pass.
Rigibore’s RADS software allows the design of back boring and eccentric tools for particular applications. Furthermore, it has the ability to apply carbide support pads on long boring operations which minimises vibrations. Delivery is typically 4-6 weeks from customer approval.
Special Tool Benefits: –
Reduced Cycle Time
Value for Money
Enhanced Process Reliability
Improved Part Quality
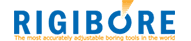
Boring Tool FAQs
What is Boring (Manufacturing)?
Boring in machining is when a pre-drilled hole is made larger using a single-point cutting tool. This process can be used to cut a tapered hole but is typically used to achieve a higher degree of accuracy for the hole’s diameter. Boring is turnings internal-diameter equivalent.
What Are the 5 Boring Tools?
There are various types of metalworking boring tools i.e. boring bars and boring heads.
Boring Bars
Tooling assemblies can incur extreme length-to-diameter ratios when boring deep holes which can lead to difficulties with stability and accuracy seen in the results. So, to not compromise on rigidity in such situations, indexable boring bars extend the tooling assemblies.
Solid Boring Bars: A more stable cut from these types of boring bars comes from the applying axial force to the dense structure. Solid boring bars are commonly made from heavy metal for roughing or carbide for finishing.
Damping Bars: Damping bars have integrated damping systems to absorb friction or counter movement and reduce chatter in long-reach boring operations.
Boring Heads
Boring heads hold cutters to enable them to rotate and cut to increase a hole’s diameter as this is what they are specifically designed for. Types of boring heads include rough boring heads, fine boring heads, twin cutter boring heads, and digital boring heads.
What Does a Boring Bar Do?
Boring is a method used in many aspects of building and a boring bar is a tool specifically for use in metalworking and woodworking. In metalworking, boring does not need to form a circular hole as the metal boring tool moves on its X or Y axes in a plunging and dragging motion, or it moves on its Z axis up and downwards. Correspondingly, movement on the X or Y axes will create an asymmetrical hole, slot, or channel, and movement on the Z axis results in an exact circular hole.
Why is it Called a Boring Bar?
A boring bar is a long tool that you will see sticking out of the tool holder and when delivering strong cutting forces, it is prone to vibrations due to its length. For that reason, the length of indexable boring bars is where it gets its name from as other cutting tools are short.