Holemaking and Drilling Tools
Sutton Tools UK Offers a Large Range of High Performance Drilling Tools That Can Meet the Challenge of a Vast Majority of Today's Manufacturing Requirements
Various ranges of drilling tools from leading brands such as Sutton Tools, MayKestag and Sphinx are stocked in-house or are available to order for delivery direct from the manufacturer. Therefore, to ensure optimum productivity for our customers, we offer timely despatch on our in-stock drilling tools. Contact our sales team on 01376 347566 to enquire about our drilling solutions.
Our hole making tools always deliver impressive performance, with standard ranges available from 3 – 80xd and micro-drilling possible from 0.03mm diameter, as well as HSS drills. The latest additions to our line-up have further added to our capability with long series hole making tools capable of greater depth up to 80xd and larger diameters. Evidently, these are just a few examples of what we achieve.
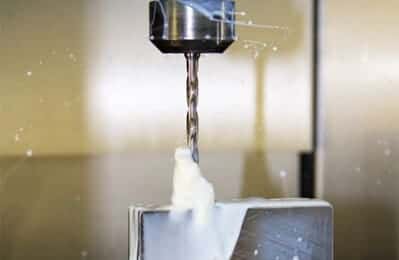
Dedicated geometries and coatings throughout our hole making tool ranges enable you to achieve maximum performance and longer tool life on all materials. Additionally, this includes the most challenging of difficult exotics as well as cast steel alloyed and non alloyed, aluminium, titanium, and cast iron.
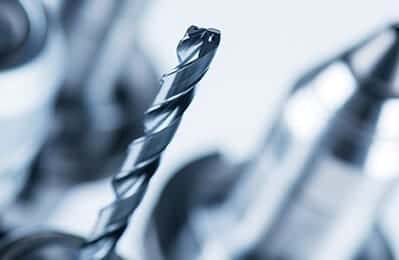
Featured Product
SPHINX ‘PHOENIX TC 2’
Achieve maximum efficiency with the Phoenix TC2 drill. With hole depths from 3xd up to 30xd, this high performance drill is suitable for a wide range of applications and is particularly suitable for difficult-to-machine and sticky materials. Also featuring polished flutes for maximum chip clearance, as well as special double-margin geometries for optimal guiding, through coolant holes and special coating, the Phoenix TC2 can achieve high feed rates, extended tool life and high process reliability, resulting in increased productivity. As a result, this reliable, high performance drill is a first choice for many.
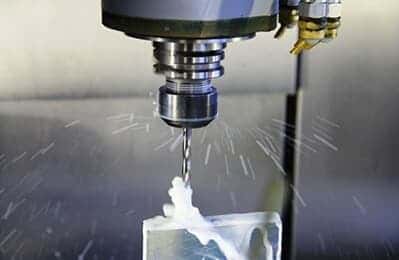
Maykestag
Solid Carbide & HSS:
- Stub Drills
- Jobber Drills
- Extra Long Drills
- Centre Drills
- Spot Drills
- Twist Drills
- Subland Drills
- Through Coolant Drills
- Deep Hole Drills
- Morse Taper Shank Drills
- Countersinks
- Reamers
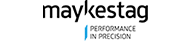
Seco
- Idexible Insert Drills
- Exchangeable Tip Drills
- Diamond Coated Drills
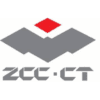
Drilling Tool FAQs
What is Drilling?
Drilling is when a hole making tool rotates in a cutting process to cut a hole in solid materials. Generally, a multi-point rotary cutting tool will be the selected drill. For the hole making process, the drilling component will be in contact with the working area and its rotational force (X revolutions per minute) of the cutting edge will cut off the swarf (chips) from the hole.
The hole making tool most commonly used is a twist drill which uses a simple, fast, and economical process to remove metal from holes and reduce chips. Accordingly, drilling is the starter process before implementing other machining processes such as boring, reaming, spotfacing, counterboring, and countersinking.
What is a Drilling Tool?
Drilling tools are end-cutting tools for use when hole making in a workpiece. For that reason, flutes and grooves form part of the shank so that cutting fluid can be fed in and chips can be removed. There are five types of hole making tool including countersink, counterbore, flat bottom boring, twist drill, and specialty.
The Hole Making Process
Holes that have been drilled are identifiable by the entrance side’s sharp edge and the exit side’s burrs. Consequently, you will typically find helical feed marks from drilling tools on the inside of the hole.
This process of hole making can cause low residual stresses around the workpiece’s hole edges, and high residual stresses on the newly formed surface. Due to these factors, the stressed surface becomes susceptible to crack propagation and corrosion under machining conditions. Therefore, a finishing operation can counteract these conditions.
Any chips of material (swarf) that are formed during the drilling process can be removed via the flutes of a fluted hole making tool. Additionally, the machinability of a material can be indicated by the type of chips produced; short chips suggest poor material machinability and long chips show good material machinability.
Thus, under machining conditions, cutting fluid is applied by flooding the workpiece and is often used in machining for several factors:
- Increase tool life
- Cool the drill
- Increase the surface finish
- Help to eject chips from the tool
- Increase speeds and feeds
Drilling In Metal
In drilling, the flute of a drill will normally carry swarf away from the drill’s tip. These cutting chips are produced by the cutting edges and will continue up the flutes and away from the hole. Therefore, the action of removing swarf is successful until the chips become jammed in the flutes which can be caused by insufficient backing off or deeper holes being drilled.
Cutting fluid can be introduced at the shank of the hole making tool through holes and can be used to lubricate the drill’s tip and ease the chip flow in machining conditions. Specifically, in cases such as when cutting aluminium, an accurate and smooth hole is gained by introducing cutting fluid as during the drilling process, the metal workpiece is prevented from grabbing the drill, resulting in greater wear resistance.
In CNC (Computer Numerical Control) machine tools, it is common practice for interrupted cut drilling or peck drilling to keep the buildup of swarf from the tool component at bay when hole making to achieve increased productivity.
What Drilling Tools Will Drill Through Hardened Steel?
For drilling through hardened steel, carbide drills are the strongest drill available. So, tungsten and carbon materials make up the Carbide compound and these carbide drills typically have a carbide tip with the rest being made from steel. Drilling steel can also be done with cobalt or titanium drills, though the drilling process will take longer.
Other Process Related to Drilling Tools
- Boring
- Counterboring
- Countersinking
- Reaming
- Spot Facing