Milling Cutters
Market-leading solid carbide milling cutters, HSS milling cutters, and indexable milling tools.
The strength and depth of our milling portfolio and the technical ability of our engineers puts Sutton Tools UK at the forefront of milling cutter suppliers throughout the UK.
Shop Milling Tools By Type
Shop Milling Cutters By Material
Our ever-expanding cutting tool portfolio allows us to supply complete tooling packages for customer projects, from conception through to completion, meeting the demands of manufacturing industries such as aerospace, automotive, medical, oil and gas, general engineering and more.
Custom Tooling

Technology

Featured Product
MAYKESTAG Speedtwister - STC end mill
Sutton Tools UK offers the all-new Maykestag ‘Speedtwister’. The Speedtwister is suited to static and dynamic milling strategies as it is specifically designed for Speed Trochoidal Cutting. With huge cutting depths of up to 5xD, high tech coating technology and optimised tool geometry for perfect chip formation, the Speedtwister provides increased productivity and profitability.
UK's Trusted Supplier of High Performance Milling Cutters
We distribute superior European-branded tools, including a selection of Milling Cutters, Groove Milling, Indexable Milling Systems, Form Milling Tools and Chamfer Milling. We’re also leading UK manufacturer of our own high-performance brand of ‘Fetoga’ solid carbide milling tools.
Maykestag
Solid Carbide & HSS:
- Mini Series End Mills
- Mini Long Series End Mills
- Stub, Standard and Long-length End Mills
- Extra Long Series End Mills
- Slot Endmills
- Ballnose End Mills
- Rippers
- Variable Helix Endmills
- Multi Flute End Mills
- Chamfer Mills
- Corner Rounding Cutters
- T Slot Endmills
- Woodruff Cutters
- Dovetail Cutters
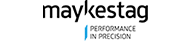
ZCCCT
- General Indexible Milling
- Disc Milling
- Face Milling
- Copy Milling
- High Feed Milling
- Helical Milling
- Square Shoulder Milling
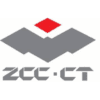
Milling Tool FAQs
What Tool Is Used for Milling?
What Are the Different Types of Milling Cutters?
In different milling applications, there are many types of milling cutters suitable for various applications. These milling cutter types include:
- Roughing end mills
- End mill cutter
- Thread mill
- Slab mill
- Ball cutter
- Radius End Mills
- Face milling cutter
- Hollow mill
- Shell mill
- Hob
- Fly cutter
- Side-and-face cutter
- Dovetail cutter
- Involute gear cutter
- Woodruff cutters
At Sutton Tools UK, we also offer a range of milling cutters for bespoke applications to general purpose needs.
Browse our shop for more information on our products.
How Do I Choose a Milling Cutter?
When deciding which milling tools you require, you will need to take into account the material that is being machined (aluminium, steel – stainless steels or alloy steels, cast iron, non ferrous materials), the stock amount to be removed through internal and external profiles, the shapes of these profiles, the machine’s capabilities, and the required surface finish. You will also need to decide whether a carbide or high speed steel (HSS) cutter is suitable for it’s purpose.
Alongside these factors, a machinist will need to consider how to meet their specification at the lowest cost. The job’s cost will include the machinist’s time, the costings, the tool life, and the time the milling machine is running.